What we do

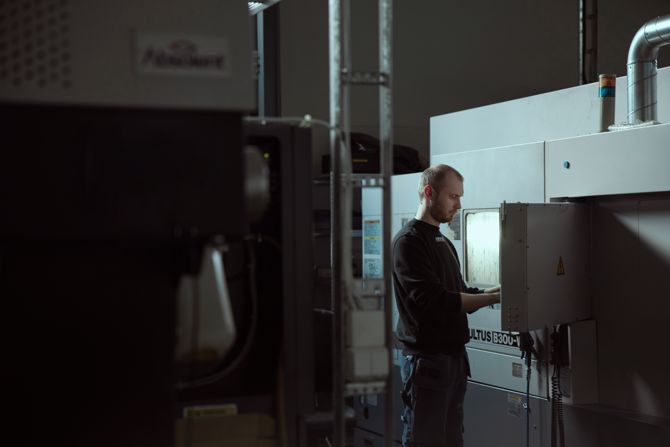
Industrial air cleaning
Clean air in production environments
When capturing and recycling harmful airborne particles and gases generated from industrial processes, we can create a sustainable and healthy environment for industrial staff. Their breaths are the reason why we exist as a company.
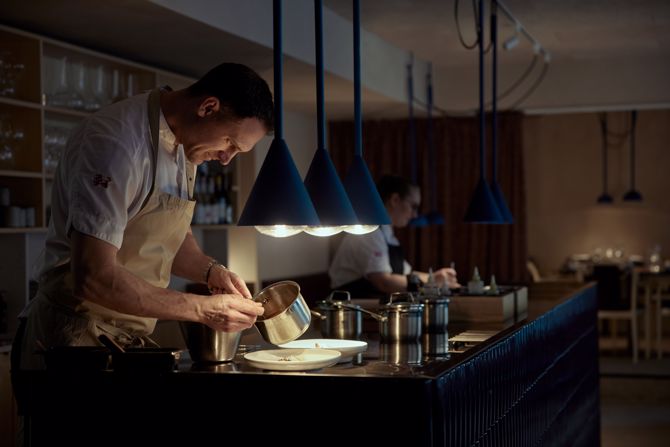
Commercial kitchen ventilation
Clean air in kitchen environments
With our ventilation systems for commercial kitchens, we force a change when it comes to future health. When removing harmful airborne particles and gases generated from cooking, professional kitchen staff can be confident the air in their working environment is clean and safe to breathe.